K.M. Packaging
KM Packaging is the leading manufacturer of food packaging. After the completion of an on-site assessment, Our engineer found opportunity to improve oil drain interval (ODI) of the crank shaft and bearing change can be extended. Lubrication performance was monitored via using Mobil Serv Oil Analysis.As a result, KM packaging can increase paper cups productivity to 4.8 million cups annually. Estimated productivity values of US$167,600 per year. Oil life is extended from 6 months to 12 months. Estimated lube oil saving value of US$14,400 per year. In addition, maintenance man hours can be reduced by 45 man-hours, leading to the total benefit of US$ 182,000
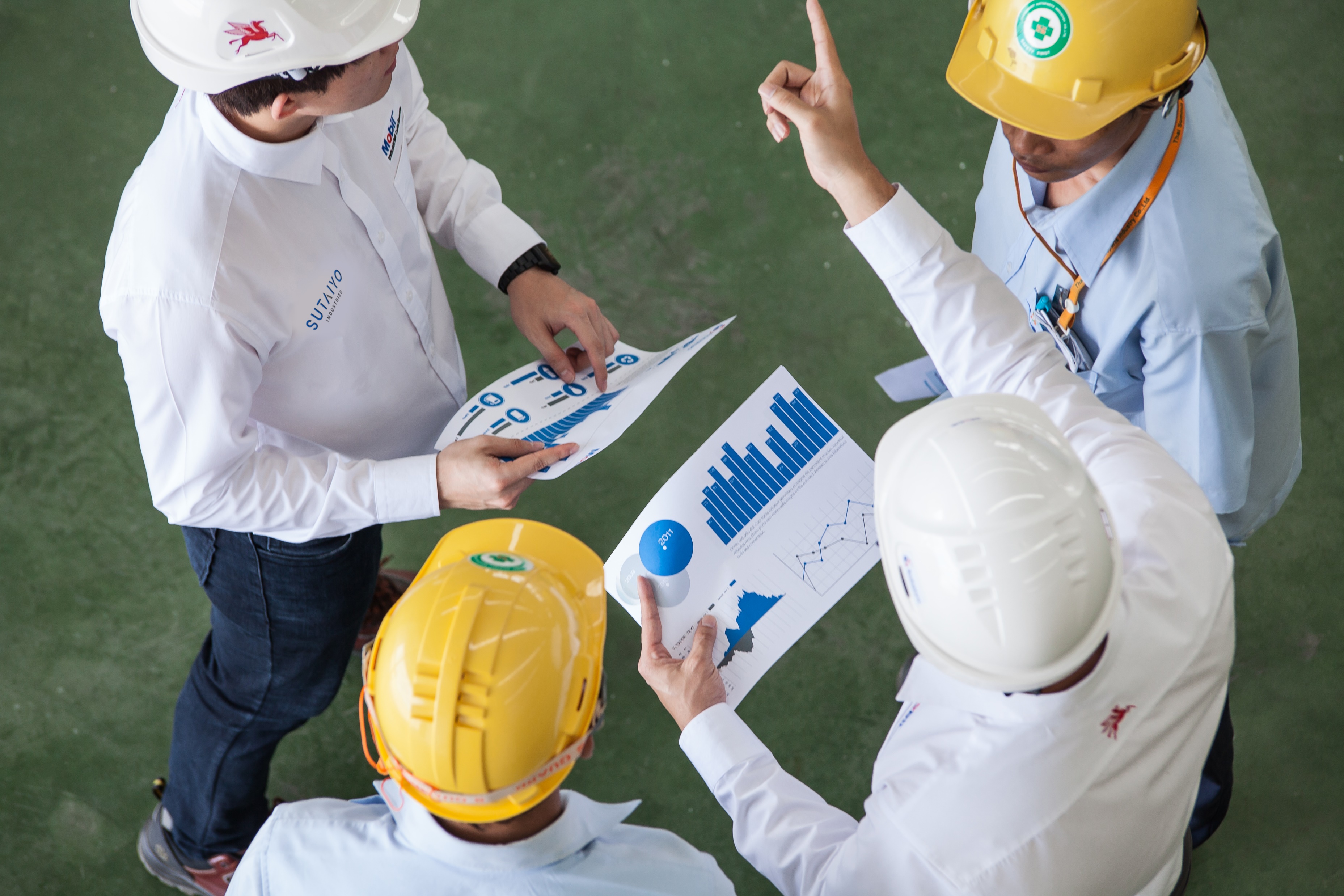
1. Assessment of Current Situation
A comprehensive evaluation is a vital first step for any organization looking to start a reliability program or benchmark their current efforts. Sutaiyo will help you understand your current lubrication and machine maintenance activities and problems through our field experience and professional knowledge and decide what changes can be made to maximize your operational performance.
The purpose of the Reliability Assessment of Sutaiyo is to create a starting point and benchmarks, finding possibilities for improvement. A valuable blueprint for applying or enhancing your reliability program will be the output.
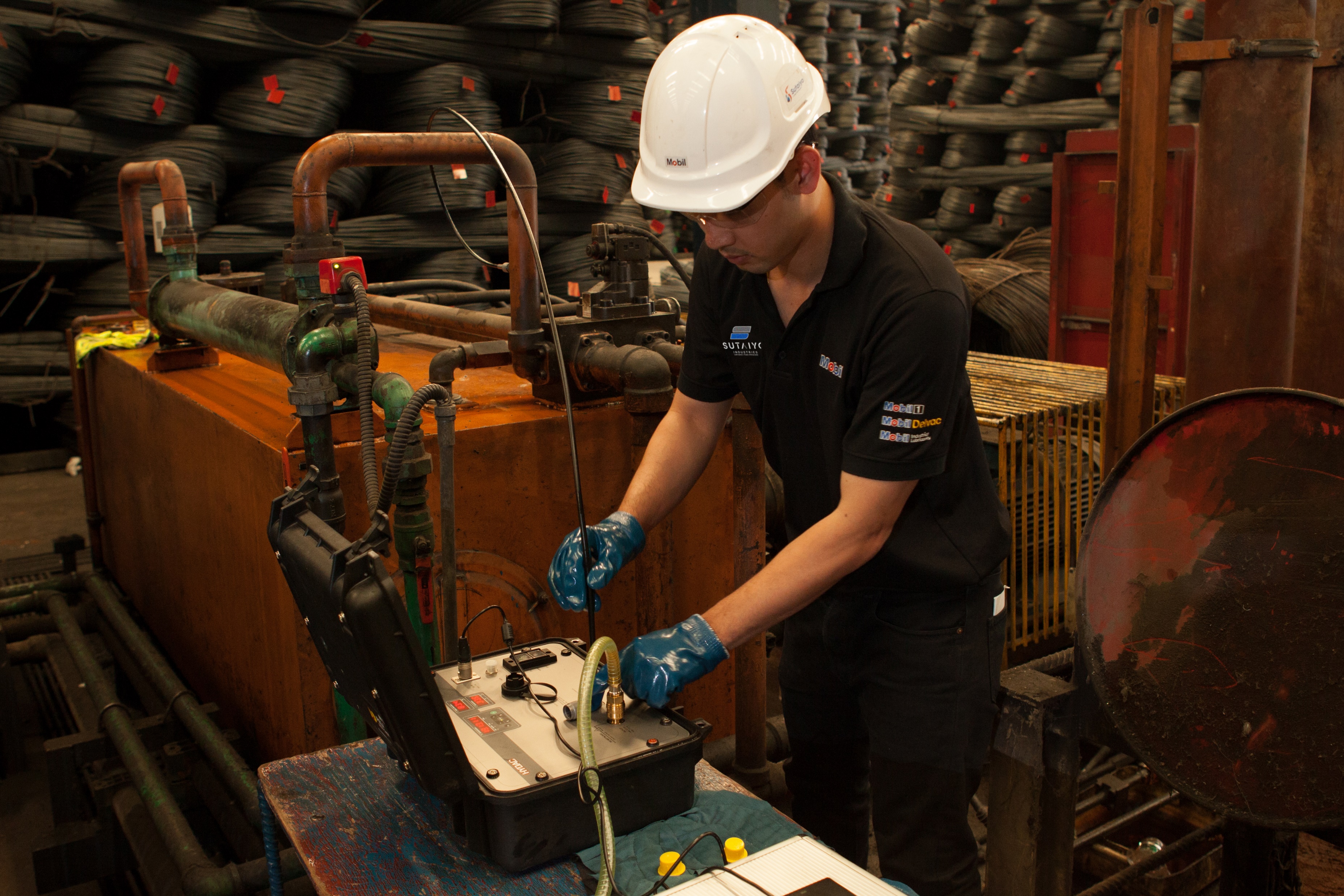
2. Detection and Measurement
Good monitoring of the oil and machine condition is essential for the effectiveness of every reliability program. An oil and vibration analysis program can help you improve your outcome with less energy consumption, fewer parts stock, less use of lubricant which need disposal, less labor, and less downtime with constant, precise monitoring of the condition of your oil and vibration of your machine, in an engine, gearbox, circulating system or main power generation motor.
Using one of the oils and machine condition monitoring programs of Sutaiyo helps you to be more successful. We track main constants for mechanical, operational, and environmental factors that can impact tools' lives.
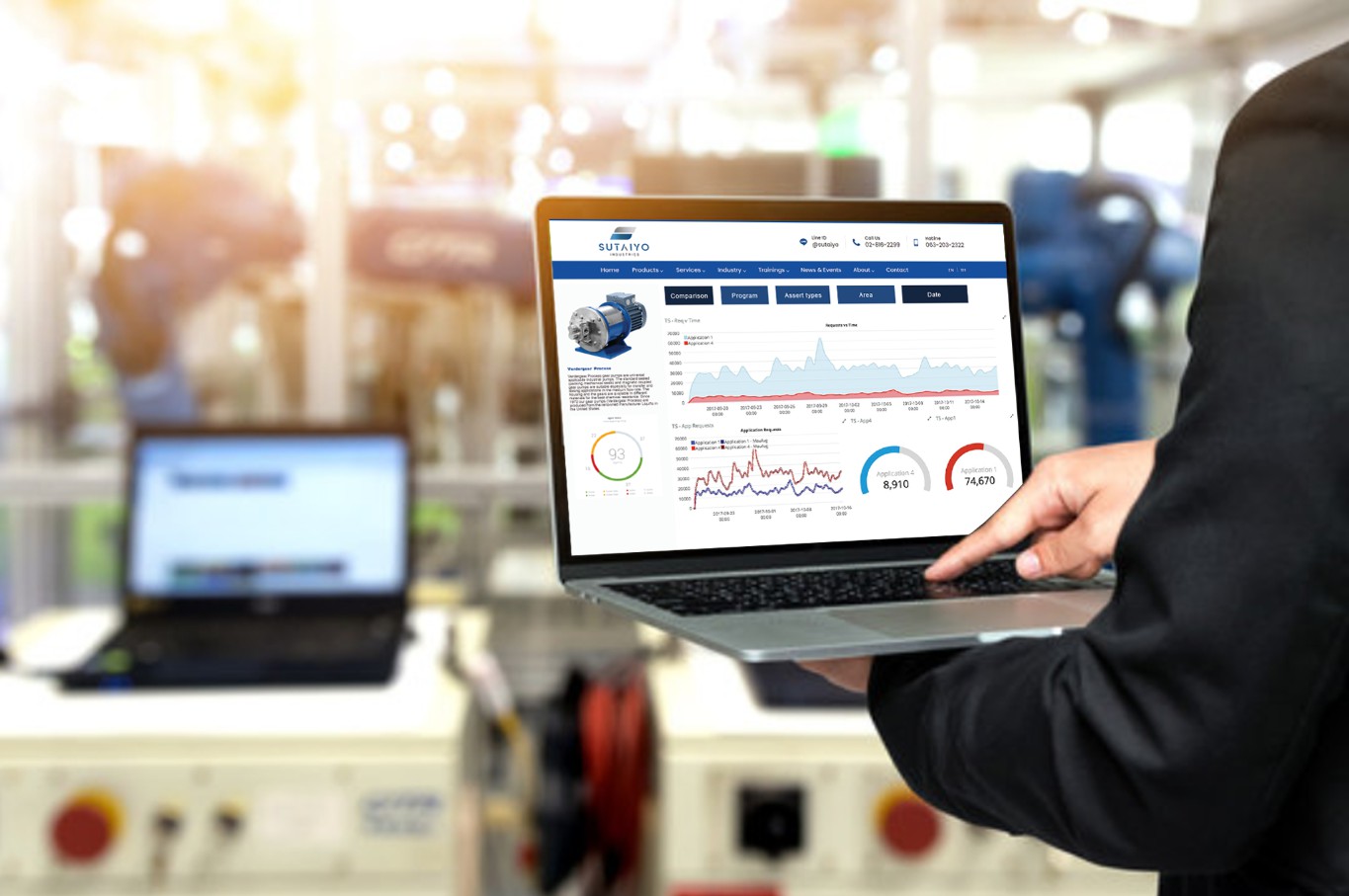
3. Cause Analysis
It is essential to understand machines' vibration and oil condition characteristics to take suitable measures against irregular conditions. It is necessary to identify the main causes of the issue and understand the effect that any action will have on the properties of the oil and vibration related to the loads to which it is subjected. For particular faults or defects, we may also perform root cause analysis. We have integrated professional knowledge and modern measuring tools in our analysis service to help you accomplish this.
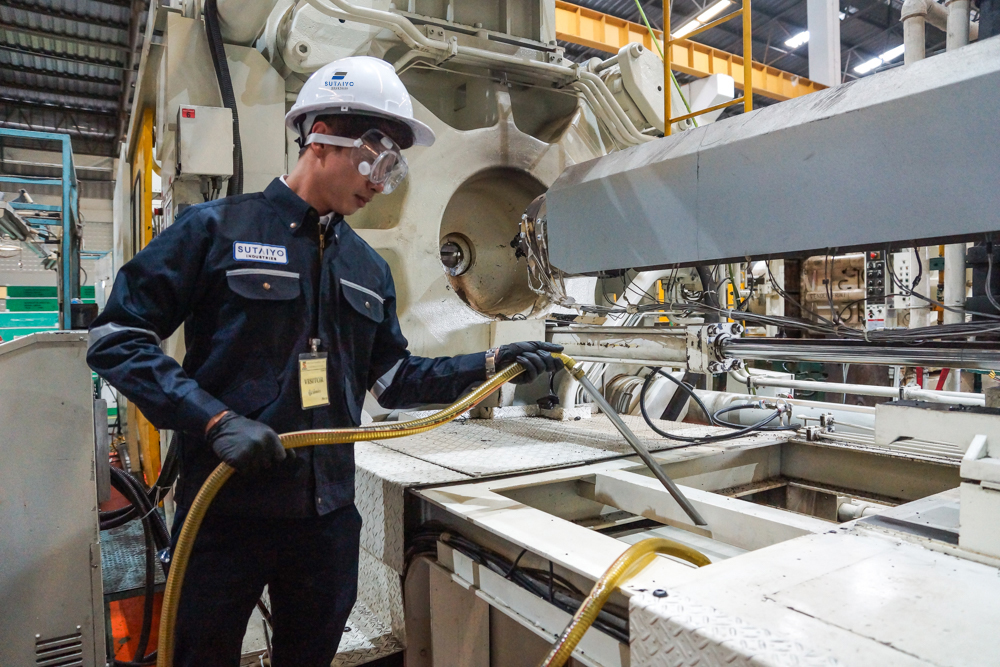
4. Improvement Solutions
Professionals of Sutaiyo will suggest enhancement strategies tailored for your operation after identifying the irregular condition's main cause. To help you enhance reliability, efficiency, and sustainability through our technological enhancement solution, either you want to improve oil conditions; oil cleanliness, removing water and particulate impurities, or varnish; improving mechanical maintenance, precision balancing, precision alignment, mounting and dismounting, etc.